I don't think stress concentrators are the main reason for a perfect spherical shell being able to withstand higher external pressure than an imperfect spherical shell in this case. According to the Wikipedia article quoted by the OP, the hull was shaped to a sphere "for enhanced buckling stability". Buckling is a form of failure of vessels under external pressure. One can watch a video of a rail car tank collapsing due to buckling.
The critical pressure of a perfect thin spherical shell for buckling is $$p_{cr}=\frac{2 E h^2}{\sqrt{3(1-\mu^2)}R^2},$$
where $h$ and $R$ are the thickness and the radius of the shell, and $E$ and $\mu$ are the modulus of elasticity and the Poisson’s ratio of the material of the shell.
Let us look at the following figure. Let us assume that the initial perfect spherical shell is between the green and the blue lines. Let us also assume that a relevant imperfect spherical shell is between the green and the orange lines. Then machining the imperfect spherical shell to the new perfect spherical shell between the green and the red lines can actually increase the critical buckling pressure as imperfections can easily reduce the critical buckling pressure of a spherical shell by a factor of 0.2, so the shell between the green and the red lines will have lower $p_{cr}$ than the shell between the green and blue lines, as it is thinner, but it can have a higher $p_{cr}$ than the shell between the green and the orange lines.
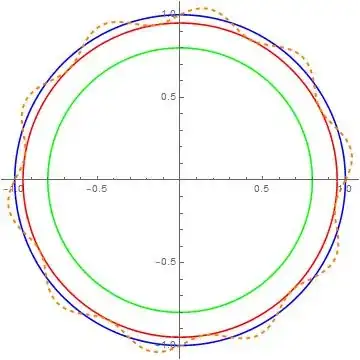